VACUUM INDUCTION MELTING FURNACES (VIM)
Processing Application:
– Equiaxed/Directional Soldification/Single Crystal Casting
– Alloy casting
– Electrode casting
– Cold Wall Induction casting (CWI)
Advantages:
– Combination DS/SC/Equiax equipment offers industry’s fastest process conversion
– Multi-zone mold heaters
– One- or two-axis precision pouring (auto teach, profile and constant volume)
– Precisiontemperature measurement (OPTO-TC)
– Closed loop solidification control
– Door-mounted furnace melt box assemblies
– Horizontal bar feeder assembly includes X-Y motion control for simultaneous loading of bars and liners or alternate bar loading via rotation
– Unmanned startup and/or shutdown of vacuum equipment (Sentry package)
– Video systems provide improved process monitoring and control
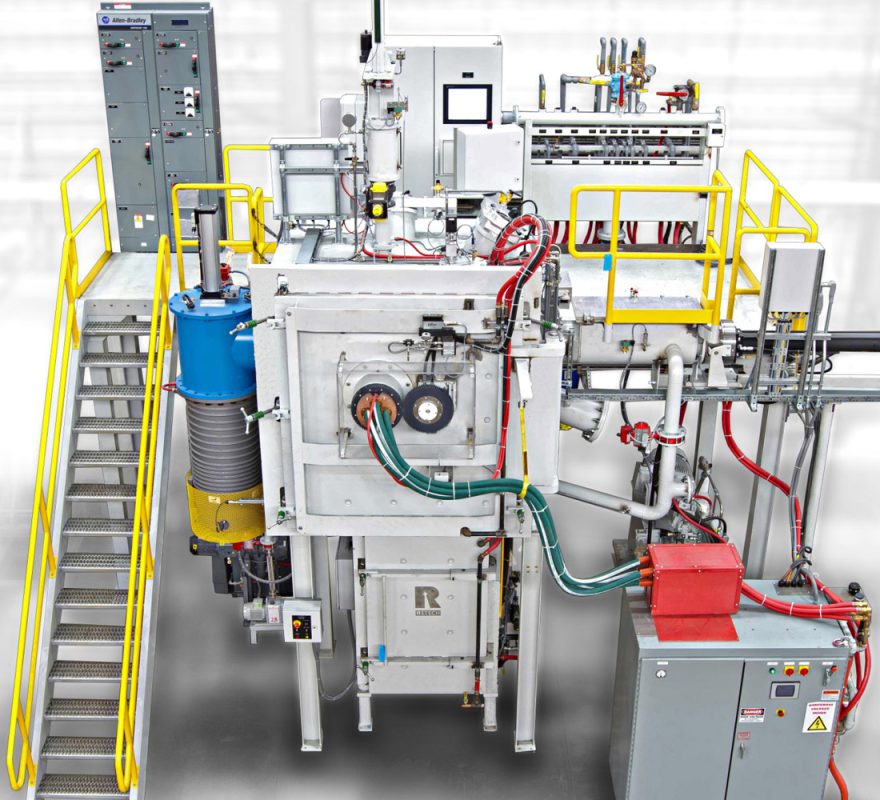
VACUUM ARC REMELT FURNACES (VAR)
Processing Application:
Ingots: Titanium, Steel, Nickel, Zirconium, Tantalum, Tungsten, Niobium
Advantages:
– Furnace design minimizes facility height requirements
– Typical ingot sizes range from 2″ to 50″ diameter (50 to 1,270 mm)
– Typical power capacities from 500 amps to 50,000 amps
– Highly accurate weight monitoring system
-X-Y electrode positioning
– Fully coaxial power entry available on all Retech VAR melters
-State-of-the-art controls with sophisticated algorithms and controls capabilities for voltage, drip short and melt rates
-Comprehensive data acquisition systems for complete melt histories
– Box column rotation
– Smooth and accurate ram position control
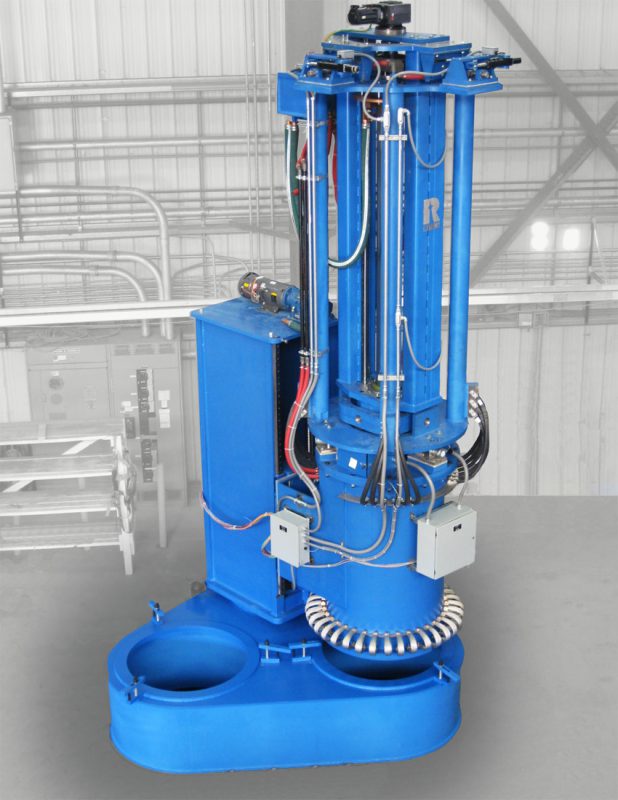
ELECTRON BEAM FURNACES (EB)
Processing Application:
-Ingots, Slab
– Scrap Consolidation Hearth Melting
– Hearth Malting
– Electron Beam Welder
Advantages:
– Includes Von Ardenne Electron Beam Guns
– Wide size range; typical 2-½ inches to 36 inches diameter (60 mm to 900mm) ingots, as well as jumbo slab production
– Multi-gun power from 80 kW to 5000 kW
-Systems of single or multiple gun design
– Winbeam® computerized beam controller offers user-friendly furnace automation
– Accepts a variety of feed material configurations, such as scrap, sponge and bar
– Offers significant cost savings by eliminating electrode welding and the consumable arc processing
– Electron beam cold hearth melting proven to eliminate high density and low density inclusions in titanium alloys
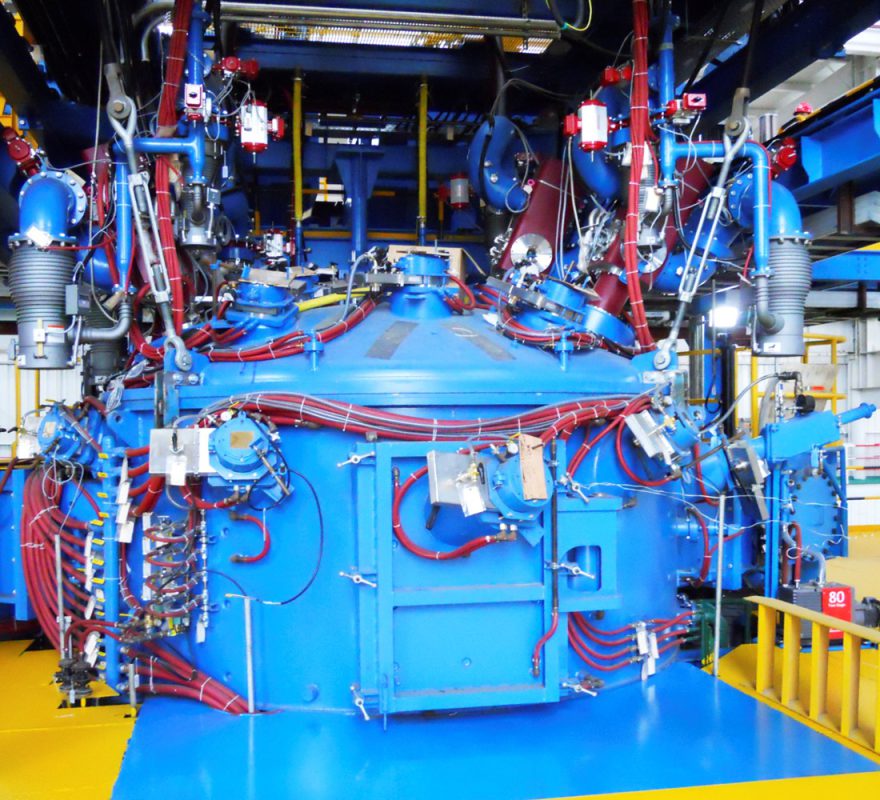
PLASMA ARC FURNACES (PAM)
Processing Application:
– Ingots, Slab, Powder Production
– Scrap Consolidation
– Hearth Melting Powder
– Plasma Welders
Advantages:
– Fine-grain ingot microstructure
– Maintains chemical composition of complex alloys
-Plasma cold hearth melting proven to eliminate high-density and low density inclusions in titanium alloys
-WinTorch® computerized torch motion profilers offer user-friendly furnace automation
-Accepts a variety of feed material configurations, such as scrap, chips, sponge, compacts and bars
-Offers significant cost savings by eliminating electrode welding and primary consumable arc processing
– Torches operable on a variety of gases, including helium, argon, nitrogen and hydrogen
-Gas recovery and reuse systems with full range of capacities available
– High throughput refining technology Typical power from 75 kW to 3000 kW Wide product range; typical sizes 2-½ inches to 36 inches diameter (60 mm to 900 mm) ingot capacities
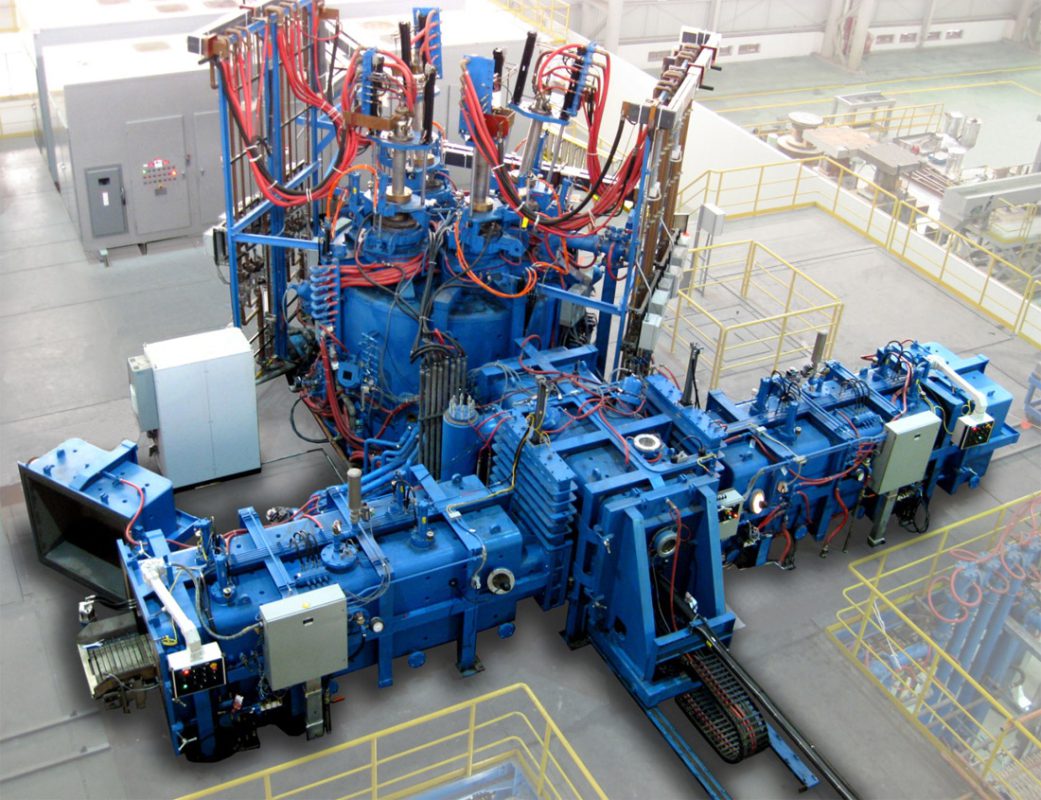
POWDER PRODUCTION EQUIPMENT
Processing Application:
– Battery Alloys
– Magnet materials
– Aerospace material
Advantages:
– Laboratory- to production-scale units available
– Spherical powder 10 microns and larger
-Thin strip casting capabilities
– Typical production rates from 1 to 20 pounds per minute (5 to 9 kg)
– Rapid solidification process
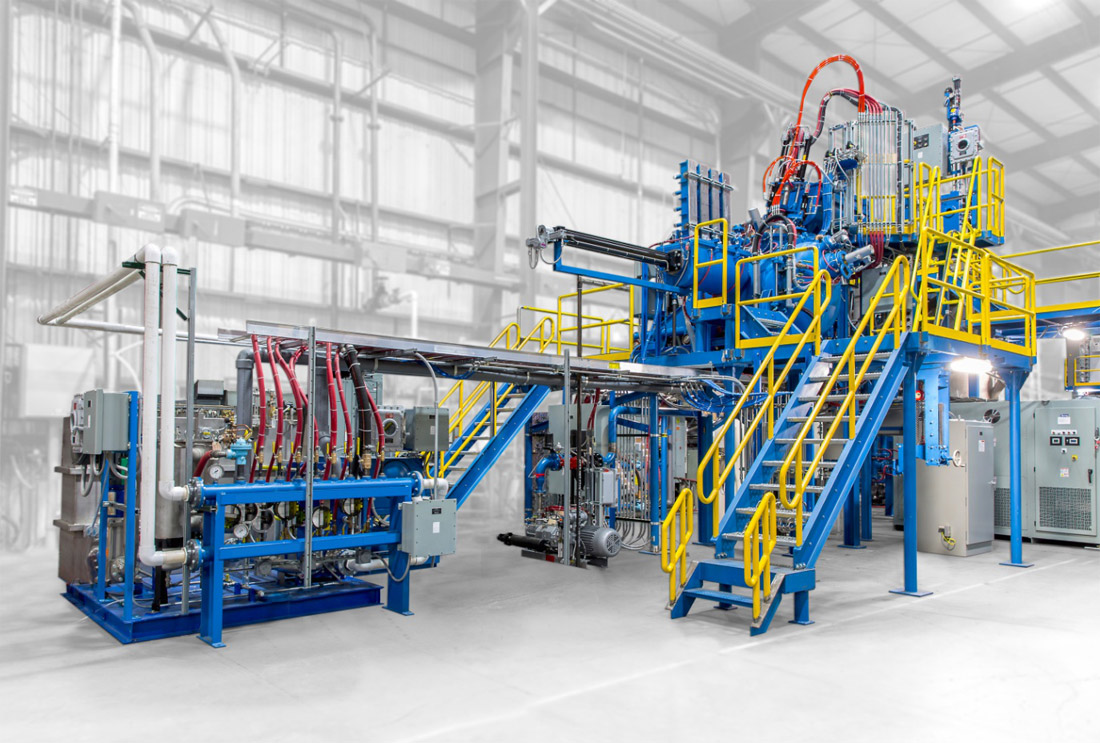